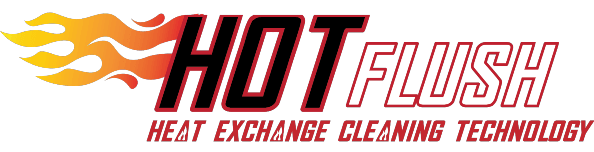
What is Hot Flush?
The Hot Flush machine pumps heated cleaning fluid through the oil cooler, with the direction of flow instantly reversing every 3 seconds for a quarter of a second.
The machine is ran until the 10 Micron check screen on the out-bound flow shows no debris. Hot Flush does not consider an oil cooler clean until nothing larger than 10 Microns in size is coming out of it. Compare this with the filtering efficiency of your average spin-on type, disposable oil filter which is effective down to a particle size of roughly 30 Microns.
Most oil cooler manufacturers have a recommended overhaul interval of every 300 to 400 hours of operation, or every two to three years (whichever comes first). Engine manufacturers generally recommend that the oil cooler be overhauled along with the engine at the end of each TBO (time between overhaul) cycle.
Hot Flush should be used anytime there has been metal contamination of the engine oil, whenever any major engine work has been conducted, or in the event of abnormally high oil temperatures when no other causes can be found.
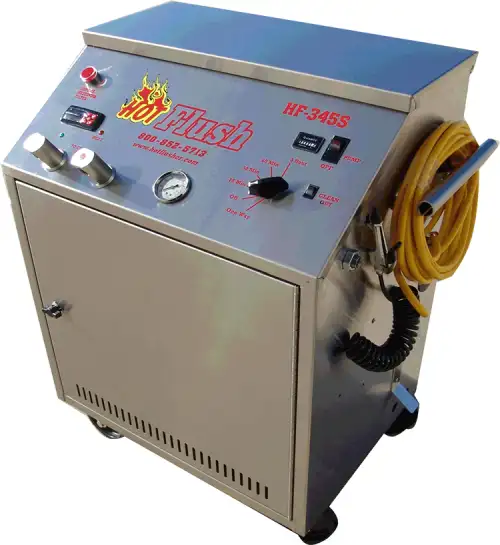
Save Time and Money
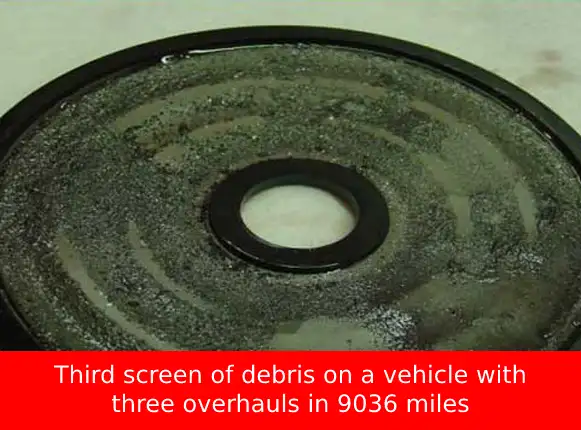
Anyone who owns or works with heat exchangers or oil coolers can benefit from Hot Flush. The cost saved from costly equipment breakdowns can more than pay for the Hot Flush machine. And, when your reputation is on the line; or customers need to be served; settling for less is simply out of the question.
In addition to saving money via preventive maintenance, Hot Flush uses standard automatic transmission fluid—not an expensive cleaning agent. This alone could more than justify the cost of the Hot Flush machine.
Many of our Hot Flush customers are in the transmission repair industry. Hot Flush helps them by reducing the number of returned vehicles, and by giving them another valuable service that they can monetize. The debris in automotive transmission coolers can easily cause a valve to stick; removing it is therefore essential. And, debris visible on the checkable cleaning screen can be shown to clientele, allowing them to make the decision for further investigation of their problem.
No matter what your industry, being equipped with a Hot Flush machine can help optimize your repair and maintenance processes!
Why Hot Flush is so Efficacious?
Hot Oil is an excellent carrying agent of debris. The viscosity of it actually grabs hold of foreign material and carries it with it. The molecules surround the debris, preventing it from becoming attached to its surroundings.
The detergents in automatic transmission fluid also help to clean away varnish when under agitation.
Solvents, which other machines use, do little to carry away debris that are under these conditions. It actually dries up the environment that the debris is in, causing it to cling to its surroundings.
The only way to dislodge the material that gets caught in the webbing of the cooler is by completely reversing the flow for a micro second! The split second reverse is just long enough to dislodge the debris!
Pulsating pumps that fluctuate between 0-40 PSI, because of the slowness of the action, has little effect by the time it reaches the cooler and does nothing to dislodge debris!
The problems that face tehnicians are they can’t take a cooler apart and clean it. They can’t see the debris, and they can’t get at it with a tool. A contaminated cooler will cause the transmission to fail! There can be enough debris in it to easily cause multiple comebacks. With traditional methods of flushing all they can do, at best, is make an educated guess as to whether or not the cooler is clean.
With your reputation on the line, can you afford such a guess.
The high speed, computer controlled flushing action is the only way to remove the debris that gets caught in the thousands of “traps” inside the cooler. Combine that with the patented process of being able to see the debris as it gets caught in the 28 micron checkable catch screen and you eliminate guessing.
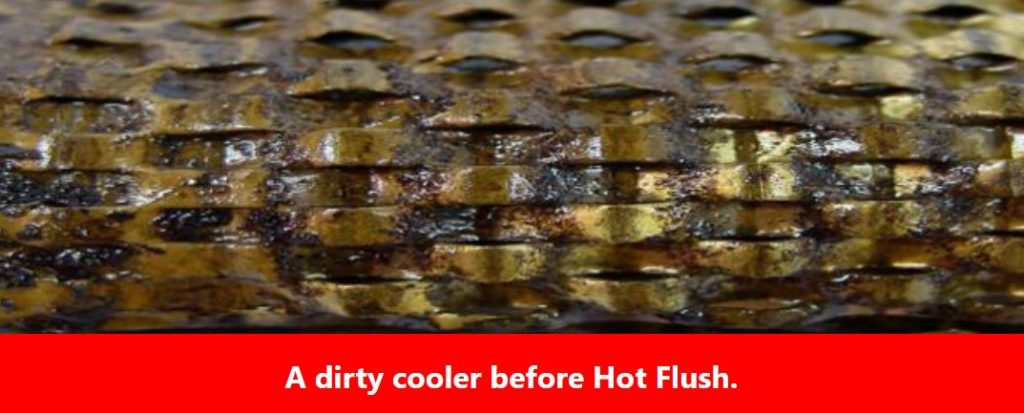

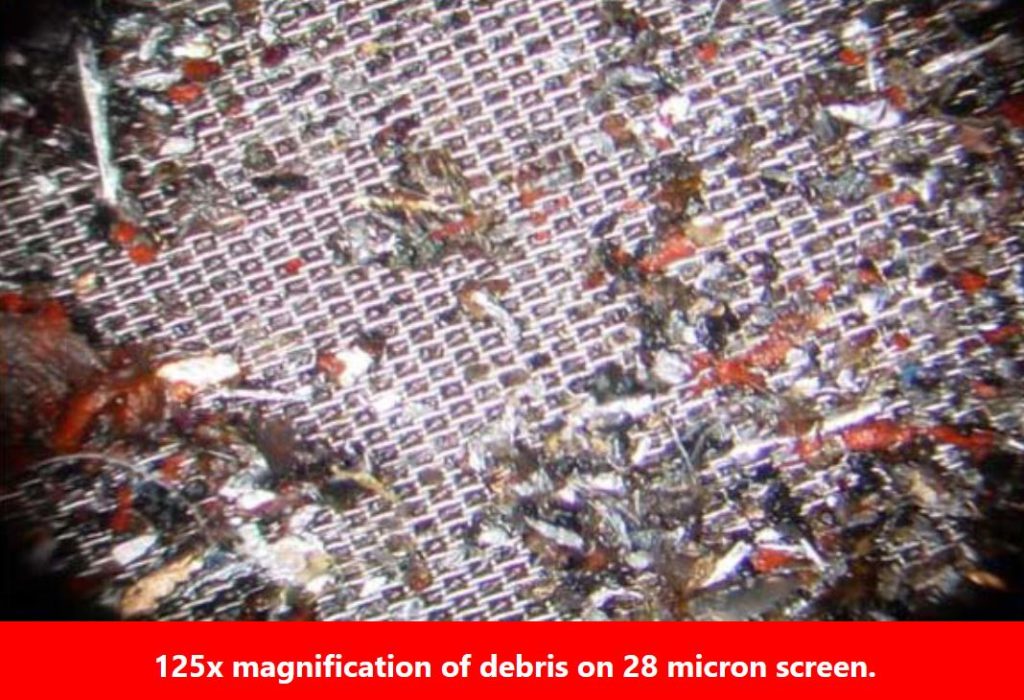
HotFLush Videos
Transmission Flushing / Cleaning Tutorial using Hot Flush
Transmission Flushing / Cleaning Tutorial using Hot Flush
Hot Flush Machines & Features
Standard Features
- #28 micron checkable cleaning screen (PATENTED) let’s you see what’s coming out of the cooler and when it’s done giving up debris.
- 10 micron 50 micron reservoir filter.
- High speed, computer controlled flushing process (PATENTED) flow reverses in 1/10th of a second, for a ¼ second, every 3 seconds (just long enough to dislodge debris) and then keep it moving through the cooler.
- Regular automatic transmission fluid, heated to 185° – 195°, is an excellent carrying agent (PART OF THE PATENTED PROCESS).
- Built in flow meter helps you gauge the progress of the contamination removal and verifies adequate flow rate.
- Auto shut off timers (4 presets)
- Dirty Filter – Automatic Shut Off
- Clean out switch purges oil from cooler.
- Pump flow rate from 4 to 80 GPM (depending on the size of machine you use).
- 120 PSI automatic air injection.
- Air hoze and nozzel.
- Digital temperature gauge.
- Pressure gauge.
- Cleanout switch (purges system).
- Preset oil pressure: 80 PSI maximum.
- Reservoir capacity ranges from 4 to 100 gallons (depending on the size of the machine).
- Air requirement: 120 PSI.
- WARRANTY: All units come with a warranty.
Optional Features
- Laser particle counter
- Infrared Thermal Camera (visually shows dislodged debris)
Hot Flush Machine – 345S
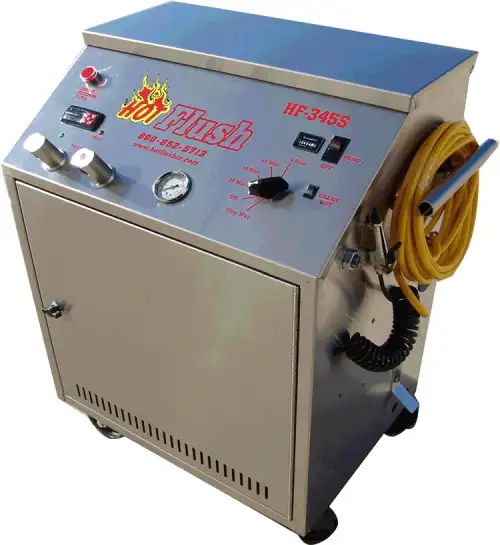
Hot Flush Machine with Clam Shell
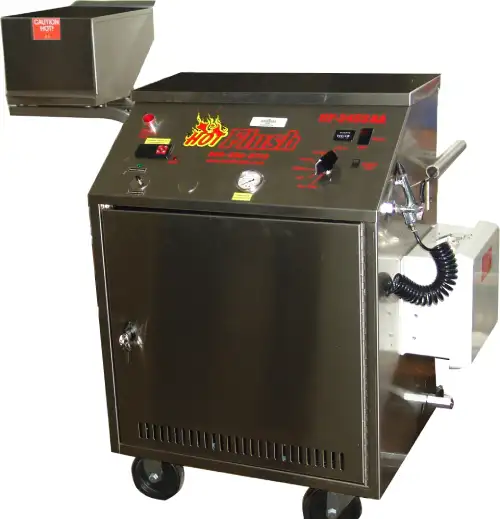
Hot Flush Machine with Enclosed Cabinet
